Control engineering of a Wire and Arc Additive Manufacturing (WAAM) process
In cooperation with ISAF, an additive manufacturing process, commonly known as "3D printing", is being investigated. Initially, these processes were mainly used in the field of rapid prototyping due to high investment costs and low production speeds. Currently, they are increasingly being used throughout the entire manufacturing process. The advantages are especially the high flexibility and the almost complete material utilization. The various processes differ in the type of material and energy supply.
The material is supplied in the form of a powder or wire. Energy is supplied by means of an electron beam, a laser or an arc welding process. The latter offer the highest build-up rates, but require complex control of the entire process. The generation of complex geometries using WAAM is state of the art, but the consideration of the generated material properties and the robustness against process disturbances is not.
The material properties of a metal depend strongly on the materials used and the cooling process. Controlling of the process can enable the desired material properties to be set. However, welding processes are susceptible to disruptions, for example disturbances of the shielding gas jacket, the welding filler materials or the interpass temperatures. In order to achieve robustness of the process against this, a consideration of those is necessary.
The metrological examination of the arc welding process enables the recording of the current temperature distribution in real time and thus the feedback of decisive process variables.
The department of Control Engineering at the Institute of Electrical Information Technology works on control and theoretical system analysis of the WAAM process under consideration of the quantities with direct relation to the material properties.
For control engineering, a control oriented model of the WAAM process is required to estimate the process variables that cannot be measured directly. The model includes the electrical quantities as well as processes at the arc, the material transfer and the heat conduction processes in the workpiece. The control system based on this model aims at ensuring the required robustness against process disturbances and the adaptation to different requirements.
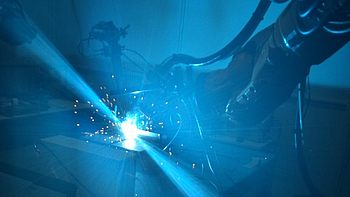